The Future of Material Testing: Innovations in Salt Spray Chambers
The Salt Spray Chamber offers a controlled environment to test the corrosion resistance strength of materials.
Salt Spray Chamber are expected to continue playing a pivotal role in the battle against corrosion. Advances in coating formulations and the development of customized, eco-friendly solutions are on the horizon. The integration of IoT technologies could also enhance the efficiency and accuracy of testing processes, offering real-time monitoring and data analysis to refine coatings and combat rust more effectively.
Introduction
Salt Spray Chambers, also known as Salt Spray Chamber fog, are critical in simulating corrosive conditions to assess the corrosion resistance of various materials and coatings. They are pivotal for industries aiming to ensure their products can withstand harsh environments, especially those exposed to saltwater or coastal conditions.
What is a Salt Spray Chamber?
A Salt Spray Chamber is a sophisticated device that creates a highly corrosive environment through the atomization and spraying of a salt solution onto test specimens. This method is essential for predicting the long-term effects of salt exposure on materials, ensuring they are fit for use in environments prone to corrosion.
How Does a Salt Spray Chamber Work?
The chamber functions by maintaining a controlled environment with specific temperature, humidity, and pH levels to ensure consistent testing conditions. Test specimens are exposed to a salt mist for a predetermined duration, after which they are evaluated for signs of corrosion.
Applications of Salt Spray Chambers
Salt Spray Chamber find extensive applications across various industries such as automotive, aerospace, marine, and electronics. They are used to test the corrosion resistance of vehicle components, aircraft structures, marine equipment, and electronic devices, ensuring these products can endure corrosive environments.
Choosing the Right Salt Spray Chamber
Selecting an appropriate Salt Spray Chamber involves considering factors like size, capacity, construction materials, control features, and safety mechanisms. It's essential to choose a chamber that can accommodate the test specimens, provide accurate control of testing conditions, and ensure the safety of its operation.
Features and Benefits of Salt Spray Chambers
Key Features
Enclosed Chamber: Prevents salt spray from contaminating the environment.
Atomization System: Controls the size and intensity of the salt spray.
Temperature and Humidity Control: Essential for maintaining consistent test conditions.
pH Control: Ensures the salt solution remains within a specific range for consistent testing.
Safety Features: Include automatic shut-offs and ventilation systems for user safety.
Data Logging and Analysis: Facilitates the recording and analysis of test results, helping users identify trends in corrosion data.
Benefits
Salt Spray Chambers offer numerous benefits, including the ability to simulate real-world corrosive conditions, thus helping manufacturers predict the durability and resistance of their products against corrosion. They also support compliance with international standards and help in the development of products capable of withstanding harsh environmental conditions.
Maintenance and Calibration
Regular maintenance and calibration are crucial for ensuring the accuracy and consistency of Salt Spray Chamber results. Maintenance tasks may include cleaning the chamber, checking solution concentration, and verifying temperature and humidity controls' accuracy. Proper maintenance ensures the chamber's longevity and reliability in delivering precise test outcomes.
Conclusion
Salt Spray Chamber are indispensable tools in the evaluation of materials' and coatings' corrosion resistance. By accurately simulating corrosive environments, they allow for the development of more durable and reliable products across various industries. Choosing the right chamber, along with regular maintenance and calibration, ensures the effective assessment of corrosion resistance, ultimately contributing to higher product quality and longevity.
What's Your Reaction?
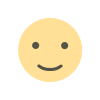
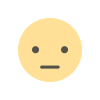
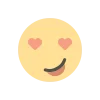
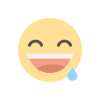
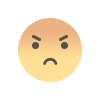
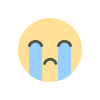
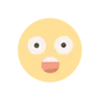